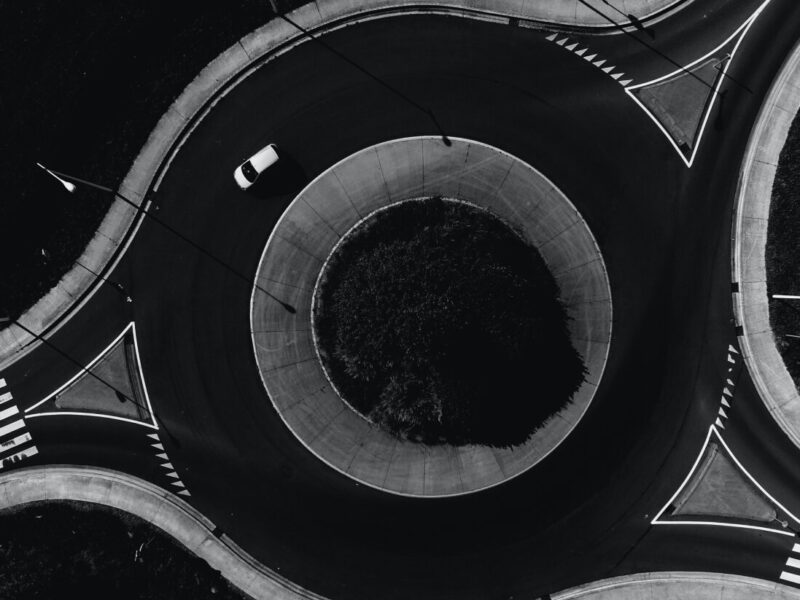
The international market in equipment, machinery and instruments is changing rapidly. Competitors from emerging markets are making inroads into the three most important global markets: US, Europe and Japan. Increased competition means manufacturers have to realign their businesses; this applies especially to their actual business models, not only their technical expertise.
Selling the best machines is not enough to maintain a stable market position. All offers must be aligned more closely with the customers’ needs and the local markets. This applies to engineering and also topics such as sustainability and environmental protection along the entire supply and value chain. Sales and service play a prominent role in localization.
The revenue and profit contribution from the service area continue to grow and in many companies already surpass the profit contribution of new products.
With the emergence of pure service providers competition is increasing. Many companies are therefore currently focusing on widening their range of services and designing future-proof service structures and processes.
From a technical point of view, the Internet of Things and the Industry 4.0 initiatives are opening up new opportunities for the areas of sales and service.
Product manufacturers are becoming service companies, taking the opportunity to design new business models and business processes, as well as specific services.
Strategic changes of this nature have to be implemented by specialists working closely with IT organizations in a target-oriented way to ensure the anticipated benefits become a reality for the business.
proaxia will help your company to fully achieve its sales and service innovation goals using the capabilities of information technology.
Machinery and plant manufacturers are placing more and more value on the technical services they provide for their plants, tools, and traction and lifting equipment. Their goal is to reduce costs and downtimes and avoid loss of production. These internal/organizational services must be of the same level of professionalism as the manufacture and distribution of the product in order to achieve long-lasting cost-savings and quality enhancement. Their maintenance measures must meet the highest standards of sustainability.
Company-wide maintenance processes can be superbly integrated and optimized through digital transformation and Industry 4.0 solutions. The same applies to inspection, servicing, repair and spare parts management. Process-oriented support in order processing and order fulfillment – from automatically generated order notification to order settlement – increases efficiency in maintenance and spare parts management.
proaxia supports your business in designing and implementing sustainable processes and solutions. We create transparency.
proaxia sees itself as the link between business and IT throughout the life cycle of your IT solutions.
Our advisers are highly specialized experts in process design for:
With our consultancy services we will help you to create viable concepts and work with you to ensure they are successfully implemented.
In the area of “Discrete Manufacturing” we offer individual services with a focus on marketing, sales and service as well as digital innovation (eBusiness).
Follow the links below for more information on our consulting services:
The opportunities presented by digitization and the Internet of Things are having an increasing influence on business models and processes. Leading companies use remote services to position their service business successfully which secures their standing as pioneers.
The opportunities presented by digitization and the Internet of Things are having an increasing influence on business models and processes. Leading companies use remote services to position their service business successfully which secures their standing as pioneers.
Look into the opportunities for a digital transformation in your own business.
In a half-day “in-house experience sharing session” we compile with you an initial analysis of the current situation and identify the actions required in your company.
What impact does digitization already have in your industry?
What benefits does digital transformation hold for your company, what added value for your customers?
What are the proven approaches for implementing “digital transformation”?
With our tried and tested approach we can give you targeted assistance with the initial assessment as well as with planning and implementing digital transformation.
Business unit and digitization strategies
Operating Models
Business Transformation Roadmaps
IT Strategies
Process, organization and master data improvement
Digital Transformation & e-Service Design
Mobilization of processes
Target, solution and integration architectures
SAP Hybris C4C for sales and service transformation
Portal solutions with SAP Hybris Commerce and SAP Fiori
Enterprise processes in SAP ECC and S/4 Hana
Upgrade and transition services (e.g. ECC to S/4 Hana)
Portfolio, program and project management
Global rollouts
Requests for proposals (RFI / RFP)
Test and quality management
Procedures and models
Headquartered in Zug, Switzerland, HOERBIGER group is active throughout the world as a leading player in the fields of compression technology, automation technology and drive technology.
HOERBIGER has redesigned the service business of wellhead compressors and has automated vital processes. The project comprises the entire process and IT integration from recording operating data to invoicing. proaxia realized the complex business logic using Internet of Things and Cloud Computing technologies and fully integrated with SAP ERP (ECC) and SAP Cloud for Customer (C4C).
“Automated monitoring, reporting and billing have now led to much more transparency. Sources of error were eliminated, and, despite the complex billing model, invoices are issued without delay, paid more rapidly and our liquidity is thus improved”
– Thomas Kriechbaum, Chief Process Officer, Executive Vice President Processmanagement and IT
Krones – the market leader in machinery and complete lines for the beverages and liquid food industry reorganized the processes for spare parts logistics in SAP.
With this project – supported by proaxia – various processes were standardized across plants in order to allow large-scale automation. Thereby Krones achieved considerable improvements: Transparency, speed, lean processes and more reliability.
“In this way we can plan our business exactly, delivering to our customers on schedule and give binding schedule information at all customer touchpoints. This is a significant factor in boosting customer satisfaction”
– Klaus Grimme, Head of Operations Central Lifecycle Service